Notas sobre diy
Notas sobre diy, impressão 3d, electrónica opensource, ...
Notas mais antigas estão arquivadas.
Proof of concept
Interesting robot idea.
forum: https://reprap.org/forum/read.php?185,364030
Build and Test of 2 Open Source 3D-Printed Syringe Pump Designs
Deformable Mirrors with Thermal Actuators
"Adaptive optics is applied in lasers, scientific instrumentation, ultra- fast sciences, ophthalmology and material processing. For successful use in these applications, the deformable mirrors must be simple, inexpensive, reliable and effi- cient. Most of the currently used technologies based on piezoelectric, electrostrictive, electromagnetic and electrostatic actuation are rather expensive. We report on a novel type of ultra-low-cost deformable mirror with actuators based on thermal expansion. The 19-channel one inch deformable mirror has response time of ≈ 15 s, actuator stroke of about 6 µm, temporal stability of about λ/10 rms in the visible range. The mirror has shown good correction ability for low-order Zernike polyno- mials, therefore it can be used for correction of rather large aberrations with slow changing amplitudes in both temporal and spatial domains."
3D printing of ecologically active soil structures
"This study investigates the feasibility of 3D printing soil structures that could support plant life. Stand-alone soil structures were successfully printed without additives using an extrusion method. When the water content is properly controlled, the printed structures are able to support germination and growth of plants. Additionally, we show that the water retention capabilities of printed structures differ from potted soil of the same composition. In three different soil textures, we correlate the drying characteristics with the ability of the soil to support plant growth, and show a fundamental difference in the soil-water characteristics of the extruded soils."
Necrobotics: Biotic Materials as Ready-to-Use Actuators
"Designs perfected through evolution have informed bioinspired animal-like robots that mimic the locomotion of cheetahs and the compliance of jellyfish; biohybrid robots go a step further by incorporating living materials directly into engineered systems. Bioinspiration and biohybridization have led to new, exciting research, but humans have relied on biotic materials—non-living materials derived from living organisms—since their early ancestors wore animal hides as clothing and used bones for tools. In this work, an inanimate spider is repurposed as a ready-to-use actuator requiring only a single facile fabrication step, initiating the area of “necrobotics” in which biotic materials are used as robotic components. The unique walking mechanism of spiders—relying on hydraulic pressure rather than antagonistic muscle pairs to extend their legs—results in a necrobotic gripper that naturally resides in its closed state and can be opened by applying pressure. The necrobotic gripper is capable of grasping objects with irregular geometries and up to 130% of its own mass. Furthermore, the gripper can serve as a handheld device and innately camouflages in outdoor environments. Necrobotics can be further extended to incorporate biotic materials derived from other creatures with similar hydraulic mechanisms for locomotion and articulation."
Mini-Delta robot
"In this paper, we introduce a novel low-cost compliant gripper with two centimeter-scaled 3-DOF delta robots using off- the-shelf linear actuators and 3D-printed soft materials. To model the kinematics of delta robots with soft compliant links, which diverge from typical rigid links, we train neural networks using a perception system. Furthermore, we analyze the delta robot’s force profile by varying the starting position in its workspace and measuring the resulting force from a push action. Finally, we demonstrate the compliance and dexterity of our gripper through six dexterous manipulation tasks involving small and delicate objects. Thus, we present the groundwork for creating modular multi-fingered hands that can execute precise and low- inertia manipulations."
More info here.
Books
- Horvath, J., Cameron, R. (2020), Mastering 3D Printing: A Guide to Modeling, Printing, and Prototyping, 2nd Edition, Apress, 2020, ISBN 9781484258422
- Harrington, J., Gertz, A. (2016), 3D CAD with Autodesk 123D: Designing for 3D Printing, Laser Cutting, and Personal Fabrication, Make Community, LLC; 1st edition (February 9, 2016), ISBN-13 ? 978-1449343019
- Ford, E. (2016), Getting Started with CNC: Personal Digital Fabrication with Shapeoko and Other Computer-Controlled Routers (Make), Make Community, 1st edition, ISBN-13 ? : 978-1457183362
- Vance, V. (2019), The Patent Game: Basics & Strategies for Innovators, Entrepreneurs, and Business Leaders, Legal Technology Press, ISBN-13 ? 978-0999114421
- Shneiderman, B., Plaisant, C., Cohen, M., Jacobs, S., Elmqvist, N., Nicholas Diakopoulos, N. (2017). Designing the User Interface: Strategies for Effective Human-Computer Interaction (6th edition), Pearson, ISBN-13: 978-0134380384
- Li, J. Z. (2015), CAD, 3D Modeling, Engineering Analysis, and Prototype Experimentation, Industrial and Research Applications, Springer International Publishing, eBook ISBN 978-3-319-05921-1, 10.1007/978-3-319-05921-1
- Scherz, P. Monk, S. (2016), Practical Electronics for Inventors, Fourth Edition 4th Edition, McGraw-Hill Education, 4th edition, March 24, 2016, ISBN-13 ? :978-1259587542
- Williams, E. (2014), AVR Programming: Learning to Write Software for Hardware (Make: Technology on Your Time) 1st Edition, Make Community, LLC; 1st edition, ISBN-13 ? : 978-1449355784
- Larry L. Peterson, Bruce S. Davie, (2021), Computer Networks: A Systems Approach (The Morgan Kaufmann Series in Networking), 6th Edition, Morgan Kaufmann, 2021, ISBN: 978-0128182000
- Ries, E. (2017), ?The Lean Startup: How Today's Entrepreneurs Use Continuous Innovation to Create Radically Successful Businesses?, Penguin Group
- Ames, M., & Runco, M. A. (2005). ?Predicting entrepreneurship from ideation and divergent thinking?, Creativity and Innovation Management, 14(3), 311-315. https://onlinelibrary.wiley.com/doi/epdf/10.1111/j.1467-8691.2004.00349.x
- Reitz, K., Schlusser, T (2016), The Hitchhiker's Guide to Python: Best Practices for Development, 1st Edition, 2016, ISBN-13: 978-1491933176, https://docs.python-guide.org/
- Joseph J. LaViola Jr., Ernst Kruijff, Ryan P. McMahan, Doug Bowman, Ivan P. Poupyrev (2017), 3D User Interfaces: Theory and Practice (2nd Edition), Addison-Wesley Professional, ISBN-10: 0134034325.
- Manuel J. Fonseca, Pedro Campos, Daniel Gonçalves (2017), Introdução ao Design de Interfaces, FCA, Portugal, 2017, 3ª Edição
- Andrew S. Tanenbaum, David J. Wetherall (2010), "Computer Networks", 5th Edition, Prentice Hall, 2010, ISBN: 978-8131770221
An Integrated Design Pipeline for Tactile Sensing Robotic Manipulators2022/06/10-22:22:36
"Traditional robotic manipulator design methods require extensive, time-consuming, and manual trial and error to produce a viable design. During this process, engineers often spend their time redesigning or reshaping components as they discover better topologies for the robotic manipulator. Tactile sensors, while useful, often complicate the design due to their bulky form factor. We propose an integrated design pipeline to streamline the design and manufacturing of robotic manipulators with knitted, glove-like tactile sensors. The proposed pipeline allows a designer to assemble a collection of modular, open-source components by applying predefined graph grammar rules. The end result is an intuitive design paradigm that allows the creation of new virtual designs of manipulators in a matter of minutes. Our framework allows the designer to fine-tune the manipulator's shape through cage-based geometry deformation. Finally, the designer can select surfaces for adding tactile sensing. Once the manipulator design is finished, the program will automatically generate 3D printing and knitting files for manufacturing. We demonstrate the utility of this pipeline by creating four custom manipulators tested on real-world tasks: screwing in a wing screw, sorting water bottles, picking up an egg, and cutting paper with scissors."
PneuAct uses a machine knitting process
"PneuAct uses a machine knitting process — not dissimilar to your grandma's plastic needle knitting — but this machine operates autonomously. A human designer simply specifies the stitch and sensor design patterns in software to program how the actuator will move, and it can then be simulated before printing. The textile piece is fabricated by the knitting machine, which can be fixed to an inexpensive, off-the-shelf rubber silicone tube to complete the actuator.
The knitted actuator integrates conductive yarn for sensing, allowing the actuators to "feel" what they touch. The team cooked up several prototypes spanning an assistive glove, a soft hand, an interactive robot, and a pneumatic walking quadruped. Their devices were wrapped in a soft, yellow fabric that made them look a little bit like banana fingers."
Light 3D printed glove for rehabilitating stroke patients
"... mechanism by which customisable wearables like hand gloves can be designed, 3D printed, and controlled remotely. “The idea behind the device is that you wear something like a glove, the physiotherapist controls the device from a remote location through the internet, and makes your hands and fingers move,” describes Bid. The device can sense various hand and finger movements, and precisely detect parameters like pressure, bending angle and shape."
Criado/Created: 2018
Última actualização/Last updated: 09-10-2023 [15:52]
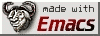

(c) Tiago Charters de Azevedo